

CommentsĪ great deal is known about the theoretical workings of emulsion breakers. Dosage is determined by the quantity of emulsified matter and normally lies between 0.5 to 1000 grams per cubic meter of water. The costs associated with breaking emulsions are greatly determined by the required quantity of chemicals and the cost price of these chemicals (the dosage level and the cost price per kilogram). The dosed chemicals are removed together with the layer of oil. Once the emulsion has been broken, the oil and/or fat particles will be removed via a follow-up step and sludge will be formed. The treatment itself does not create residual materials. Depending on the selected method, electricity or heat can also be used. The primary support products are chemicals (acids, bases, oxidators, specific polymers). In a follow-up step, very high efficiency can then be realised for the removal of oil or fat particles from the wastewater (normally via flotation, also see technical file W33). The emulsion can be fully unbound and an efficiency of almost 100% can be realised if the correct method is used to break the emulsion.
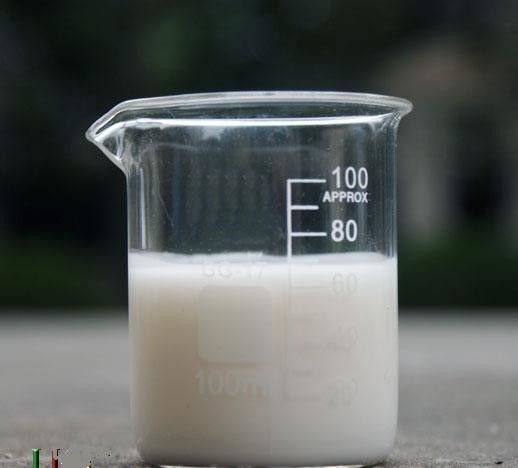
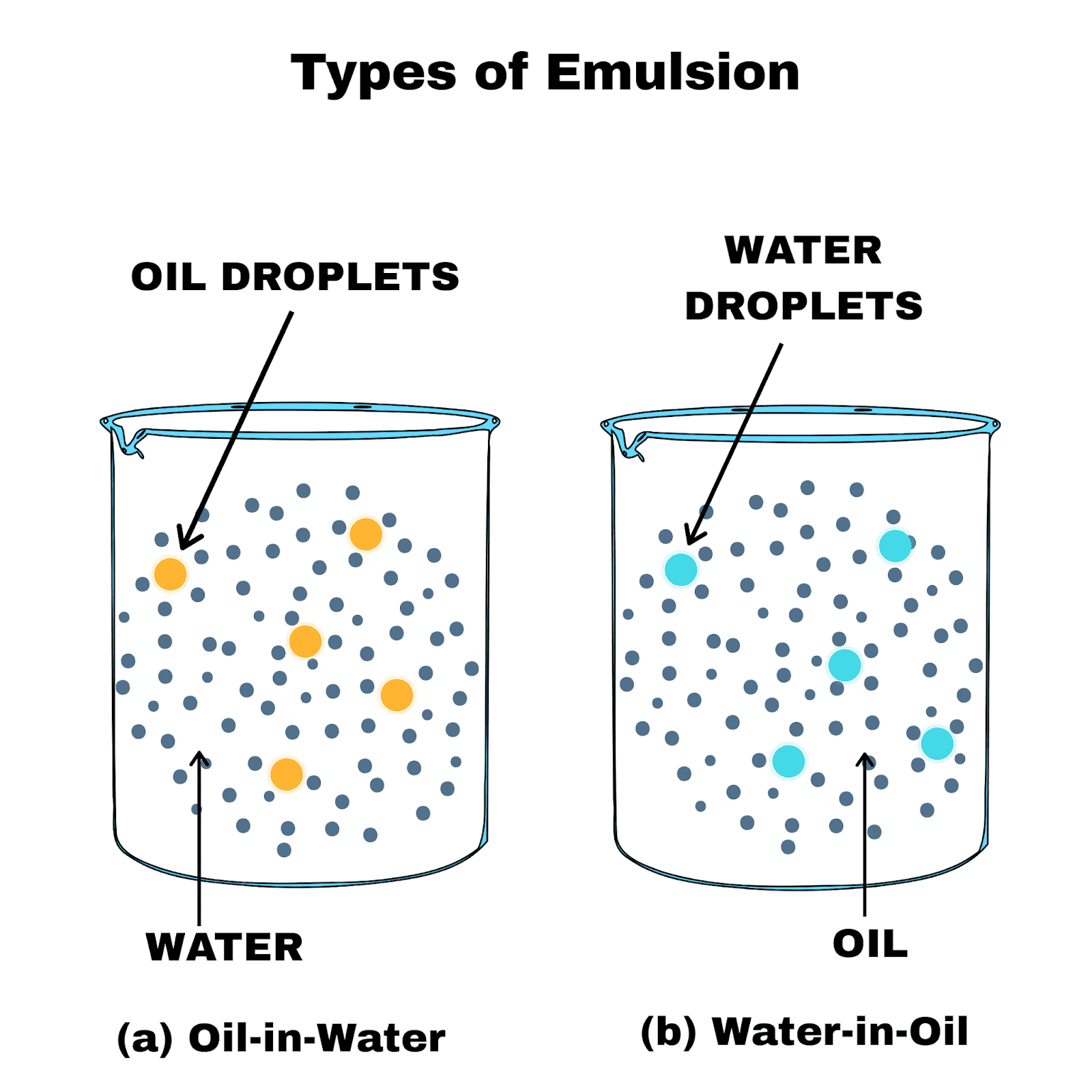
Lab tests can then evaluate the feasibility. This will allow the problem to be resolved more effectively. An analysis of the wastewater for types of oil and other substances helps to identify the emulsion’s emulsifiers. It is important to first investigate which technique offers the best solution for breaking the emulsion. The choice of emulsion breaking must also take into account additional post-treatments (e.g. Thus, if enough residual heat is available in the company, one is more likely to choose thermal emulsion breaking (if processes permit this). Other factors also play a role when selecting a purification technique.

This means that, for each emulsion, research must be carried out to determine which of the above mentioned possibilities offers the best solution for breaking the emulsion. These emulsifiers vary greatly and are specific to the type of oil or fat in the emulsion. Boundary conditionsĮach emulsion is stabilised by its own specific components that ensure the oil does not leave the solution. Emulsions are also formed in wastewater during de-salting of crude oil in refineries. An example is quenching (cooling with water) naphta gas in steam crackers. Emulsions are also frequently encountered in the chemical and petrochemical industries. Emulsions are often encountered in wastewater in the foodstuffs industry, including in the production of sauces and margarines, in the dairy industry, etc. A few specific examples of oils that cause emulsions are the drilling and cutting oils used in metal processing (steel industry, metal industry and automobile industry). ApplicationĮmulsions are encountered in many wastewater flows, often without the company being aware of them. Thus it is recommended to regularly carry out optimisation research for emulsions in wastewater. In practice, it has been demonstrated that emulsions vary greatly and must be broken in different ways: specific chemicals, doses, pH and temperature work areas, etc. A disadvantage is the large quantities of support products that are often needed for effective emulsion breaking, which makes the technique relatively expensive. Very high efficiency can be realised if emulsion breakers are used correctly. Once the emulsion has been broken, the various components can be separated using, for example, flotation, filtration, coalescence, centrifuging. Dosing chemicals that neutralise the surface load of emulsified particles.Sharply reducing pH in the wastewater, whereby the surface load of emulsified particles is reduced.Oxidising present components (like the emulsifier).Dosing chemicals that bond with the emulsifier, whereby the oil particles are no longer in emulsion.Applying an electrical current to the wastewater.Heating and then cooling the wastewater.Typical examples of oil-in-water emulsions are milk, drilling and cutting oils, etc.Īn emulsion can be broken in various ways depending on the type of oil or fat and the various emulsifiers present in the emulsion. The emulsions are stabilised by the presence of various types of chemical substances that have a specific effect on the solubility – they are called emulsifiers. It is impossible to realise oil or fat separation without an effective system for breaking the emulsion. Despite the fact that oil and water will stay apart under normal conditions, an emulsion may still be formed. This emulsion is a mix of very finely dispersed oil or fat droplets in water. The most common emulsion is the oil-in-water emulsion. Water-in-oil emulsions and oil-in-water emulsions. There are 2 types of emulsions that are encountered within industry.
